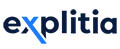
Próg wejścia – niżej się nie da
Proces zbierania danych z maszyn to jeden z pierwszych i w zasadzie najłatwiejszy krok, który powinny podjąć przedsiębiorstwa chcące sprawnie przejść transformację cyfrową swojej firmy. Próg wejścia do tego procesu stanowią zaledwie trzy elementy:
Duża firma duży problem
W przypadku mniejszych przedsiębiorstw lub nieskomplikowanych systemów, a także gdy klient nie jest pewny swoich potrzeb, próg wejścia jest rzeczywiście niski. Sytuacja wygląda nieco inaczej, gdy mamy do czynienia z dużymi firmami i złożonymi rozwiązaniami. Pojawiają się bowiem specyficzne wymagania korporacyjne oraz prawne. Do wdrożenia systemu zbierania danych z maszyn mogą okazać się konieczne informacje dotyczące wyglądu infrastruktury czy połączenia sterownika z systemem do sieci. Taka sytuacja może wymagać nieco więcej zaangażowania od klienta i prac związanych z firewall’em oraz infrastrukturą sieciową.
W przypadku większych urządzeń, które generują dużą ilość danych, istotne jest ustalenie hierarchii ważności sygnałów oraz eliminacja redundancji. Na przykład, jeżeli posiadamy dane dotyczące ilości produktów wyprodukowanych przez maszynę w określonym czasie, nie ma potrzeby generowania dodatkowych sygnałów odnoszących się do czasu cyklu produkcji. Zmienne te mogą być wyliczone na podstawie już zbieranych informacji, co pozwala na redukcję przyrostu danych w bazie. Dzięki temu serwery są mniej obciążone, co przyczynia się do efektywniejszego zarządzania zasobami systemu.
System otwarty czy zamknięty?
Wybór odpowiedniej technologii do integracji systemów jest kluczowy i powinien być dostosowany do potrzeb oraz kompetencji klienta. Systemy można podzielić na dwie główne kategorie:
Maksymalizacja produktywności, minimalizacja błędów
Przed wdrożeniem systemu automatyki do zbierania danych z maszyn, konieczne jest wykonywanie szeregu zadań ręcznie. Prowadzi to do marnotrawstwa czasu i potencjału ludzkiego. Operatorzy w zakładach produkcyjnych manualnie zbierają, dokumentują oraz analizują dane, często przepisując je do arkuszy kalkulacyjnych, co wymaga dodatkowego nakładu pracy. Automatyzacja tych procesów ma na celu całkowitą eliminację ręcznego wykonywania tych zadań, dzięki czemu pracownicy mogą skupić się na bardziej produktywnych działaniach.
Systemy automatycznego zbierania danych z maszyn nie tylko usprawniają proces dokumentacji, ale także przyspieszają reakcję na krytyczne zdarzenia. Dzięki automatycznemu wysyłaniu alarmów poprzez e-mail lub SMS możliwe jest szybkie reagowanie na ewentualne wyzwania, takie jak produkcja wadliwych partii produktów. W efekcie minimalizuje się reklamacje i zwroty, a tym samym – straty firmy.
Korzyści automatycznego zbierania danych z maszyn
Integracja systemów do zbierania danych z maszyn może stanowić sposób na optymalizację kosztów produkcji, np. poprzez dokładny monitoring zużycia mediów takich jak woda czy energia. Systemy te umożliwiają także precyzyjne śledzenie parametrów procesowych, w tym temperatury, ciśnienia, a nawet momentu skręceń śrub. Dzięki temu, oprócz identyfikacji produktów zgodnych (OK) lub niezgodnych (NOK) ze standardami, można zrozumieć przyczyny występowania błędów. Wyniki te prezentowane są w formie raportów z wykresami, które ułatwiają lokalizację najczęstszych usterek, umożliwiając ich szybką eliminację.
Dodatkowo efektywne zbieranie danych pozwala na identyfikację wąskich gardeł procesu produkcyjnego, co umożliwia wykorzystanie zasady Pareto do skupienia wysiłków na obszarach, które przy minimalnym nakładzie mogą przynieść największe oszczędności i usprawnienia.
Jednocześnie integracja systemów do zbierania danych z maszyn pozwala na precyzyjne prognozowanie zapotrzebowania na półprodukty, co umożliwia optymalne planowanie zaopatrzenia magazynów. Dzięki temu zapewnia się dostępność niezbędnych komponentów w okresach wzmożonego popytu, minimalizując jednocześnie ryzyko nadmiaru zapasów w mniej aktywnych miesiącach.
Podsumowując, rozpoczęcie zbierania danych z maszyn może być zarówno proste jak i nieco bardziej skomplikowane. Istotne jest, aby znaleźć rzetelnego i doświadczonego partnera technologicznego, który pomoże w implementacji odpowiednich rozwiązań. Dzięki automatycznemu pobieraniu danych z maszyn i opisaniu informacji w odpowiednich biznesowych kontekstach można lepiej zarządzać zasobami, szybko reagować na ewentualne trudności i przewidywać przyszłe potrzeby.
Autor: Krzysztof Gandziarowski, Developer, EXPLITIA S.A.
Źródło: www.explitia.com
Proces zbierania danych z maszyn to jeden z pierwszych i w zasadzie najłatwiejszy krok, który powinny podjąć przedsiębiorstwa chcące sprawnie przejść transformację cyfrową swojej firmy. Próg wejścia do tego procesu stanowią zaledwie trzy elementy:
- Źródło danych, czyli czujnik zbierający pożądane informacje.
- Sterownik PLC lub moduł I/O, który zapisuje dane w pamięci i jednocześnie służy jako komunikator ze źródłem danych oraz komputerem.
- Komputer/serwer potrzebny do uruchomienia aplikacji.
Duża firma duży problem
W przypadku mniejszych przedsiębiorstw lub nieskomplikowanych systemów, a także gdy klient nie jest pewny swoich potrzeb, próg wejścia jest rzeczywiście niski. Sytuacja wygląda nieco inaczej, gdy mamy do czynienia z dużymi firmami i złożonymi rozwiązaniami. Pojawiają się bowiem specyficzne wymagania korporacyjne oraz prawne. Do wdrożenia systemu zbierania danych z maszyn mogą okazać się konieczne informacje dotyczące wyglądu infrastruktury czy połączenia sterownika z systemem do sieci. Taka sytuacja może wymagać nieco więcej zaangażowania od klienta i prac związanych z firewall’em oraz infrastrukturą sieciową.
W przypadku większych urządzeń, które generują dużą ilość danych, istotne jest ustalenie hierarchii ważności sygnałów oraz eliminacja redundancji. Na przykład, jeżeli posiadamy dane dotyczące ilości produktów wyprodukowanych przez maszynę w określonym czasie, nie ma potrzeby generowania dodatkowych sygnałów odnoszących się do czasu cyklu produkcji. Zmienne te mogą być wyliczone na podstawie już zbieranych informacji, co pozwala na redukcję przyrostu danych w bazie. Dzięki temu serwery są mniej obciążone, co przyczynia się do efektywniejszego zarządzania zasobami systemu.
System otwarty czy zamknięty?
Wybór odpowiedniej technologii do integracji systemów jest kluczowy i powinien być dostosowany do potrzeb oraz kompetencji klienta. Systemy można podzielić na dwie główne kategorie:
- Systemy otwarte – oferują użytkownikom możliwość samodzielnej ingerencji w konfigurację i działanie systemu. Umożliwiają one dostosowywanie funkcji, wprowadzanie zmian oraz dodawanie nowych elementów, co daje większą elastyczność w zarządzaniu i adaptacji do specyficznych potrzeb.
- Systemy zamknięte – charakteryzują się ograniczoną możliwością interakcji ze strony klienta. Obsługą i zarządzaniem systemu zajmuje się wyłącznie firma zewnętrzna, która odpowiedzialna była za wdrożenie i utrzymanie systemu. W tym przypadku klient jest zobowiązany jedynie do utrzymania połączenia sieciowego ze sterownikiem.
Maksymalizacja produktywności, minimalizacja błędów
Przed wdrożeniem systemu automatyki do zbierania danych z maszyn, konieczne jest wykonywanie szeregu zadań ręcznie. Prowadzi to do marnotrawstwa czasu i potencjału ludzkiego. Operatorzy w zakładach produkcyjnych manualnie zbierają, dokumentują oraz analizują dane, często przepisując je do arkuszy kalkulacyjnych, co wymaga dodatkowego nakładu pracy. Automatyzacja tych procesów ma na celu całkowitą eliminację ręcznego wykonywania tych zadań, dzięki czemu pracownicy mogą skupić się na bardziej produktywnych działaniach.
Systemy automatycznego zbierania danych z maszyn nie tylko usprawniają proces dokumentacji, ale także przyspieszają reakcję na krytyczne zdarzenia. Dzięki automatycznemu wysyłaniu alarmów poprzez e-mail lub SMS możliwe jest szybkie reagowanie na ewentualne wyzwania, takie jak produkcja wadliwych partii produktów. W efekcie minimalizuje się reklamacje i zwroty, a tym samym – straty firmy.
Korzyści automatycznego zbierania danych z maszyn
Integracja systemów do zbierania danych z maszyn może stanowić sposób na optymalizację kosztów produkcji, np. poprzez dokładny monitoring zużycia mediów takich jak woda czy energia. Systemy te umożliwiają także precyzyjne śledzenie parametrów procesowych, w tym temperatury, ciśnienia, a nawet momentu skręceń śrub. Dzięki temu, oprócz identyfikacji produktów zgodnych (OK) lub niezgodnych (NOK) ze standardami, można zrozumieć przyczyny występowania błędów. Wyniki te prezentowane są w formie raportów z wykresami, które ułatwiają lokalizację najczęstszych usterek, umożliwiając ich szybką eliminację.
Dodatkowo efektywne zbieranie danych pozwala na identyfikację wąskich gardeł procesu produkcyjnego, co umożliwia wykorzystanie zasady Pareto do skupienia wysiłków na obszarach, które przy minimalnym nakładzie mogą przynieść największe oszczędności i usprawnienia.
Jednocześnie integracja systemów do zbierania danych z maszyn pozwala na precyzyjne prognozowanie zapotrzebowania na półprodukty, co umożliwia optymalne planowanie zaopatrzenia magazynów. Dzięki temu zapewnia się dostępność niezbędnych komponentów w okresach wzmożonego popytu, minimalizując jednocześnie ryzyko nadmiaru zapasów w mniej aktywnych miesiącach.
Podsumowując, rozpoczęcie zbierania danych z maszyn może być zarówno proste jak i nieco bardziej skomplikowane. Istotne jest, aby znaleźć rzetelnego i doświadczonego partnera technologicznego, który pomoże w implementacji odpowiednich rozwiązań. Dzięki automatycznemu pobieraniu danych z maszyn i opisaniu informacji w odpowiednich biznesowych kontekstach można lepiej zarządzać zasobami, szybko reagować na ewentualne trudności i przewidywać przyszłe potrzeby.
Autor: Krzysztof Gandziarowski, Developer, EXPLITIA S.A.
Źródło: www.explitia.com